When it comes to manufacturing car parts, quality control is essential. The accuracy and precision of press brake machines play a crucial role in this process.
To ensure the highest standards of safety and reliability, these machines must be calibrated properly for each part that they produce. This article will discuss how setting the standard with quality control in car parts through press brake accuracy can have numerous benefits for both manufacturers and consumers alike.
We will explore what goes into setting up such a system as well as look at some of the key advantages that come from having a reliable press brake machine in place. Finally, we touch on how developing new technologies like automated calibration systems can further enhance production capabilities while ensuring an even higher level of safety and reliability when it comes to producing car parts.
Ensuring Consistent Precision Through Proper Maintenance of Press Brakes

Ensuring consistent precision and accuracy is essential in the production of car parts, especially when using press brakes. Proper maintenance of a press brake is key to achieving desired results time after time.
The machine should be regularly inspected for signs of wear or damage that might affect its performance, such as worn seals, damaged tooling, or rust on moving parts. In addition to regular inspection, it’s important to keep up with scheduled preventive maintenance checks for proper lubrication and replacement of worn components.
To ensure top-notch quality control in car part production through press brake accuracy, operators should also follow safety procedures diligently by wearing appropriate protective gear and ensuring all guards are securely fastened before operating the equipment. Finally, investing in advanced technology such as automated width gauges can help maintain optimal levels of speed and consistency throughout each production run while minimizing costly mistakes due to human error.
Reducing Waste and Cost by Optimizing the Setting Up Process of a Press Brake
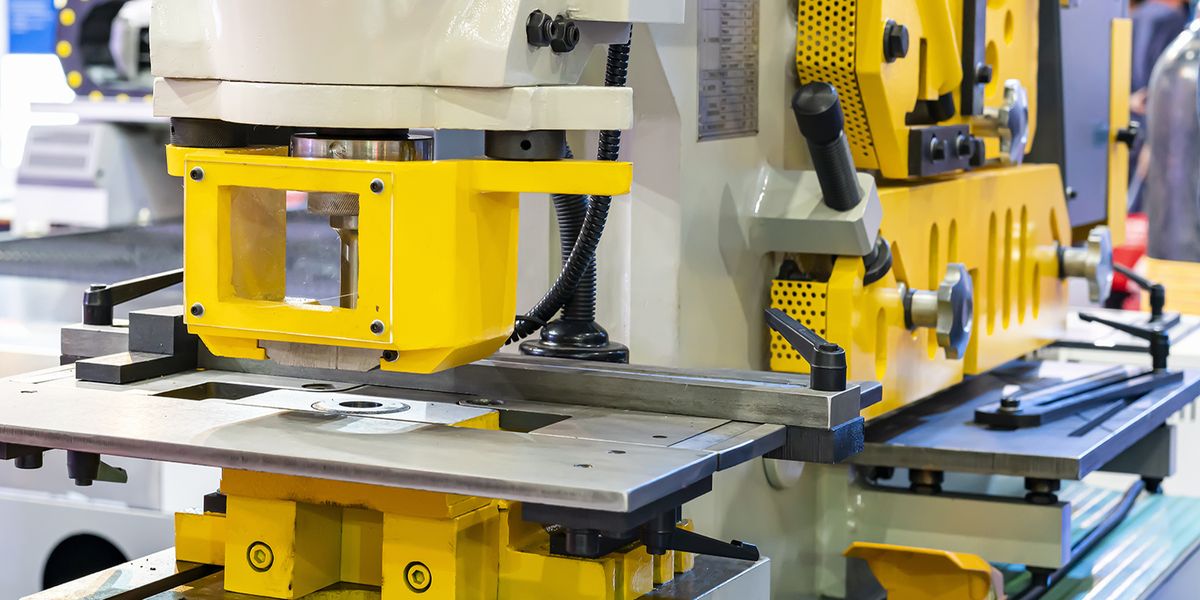
When it comes to manufacturing parts for cars, accuracy and precision are of the utmost importance. A press brake is an essential tool in achieving this level of quality control.
However, the setup process can be time-consuming and costly if done inefficiently. Fortunately, there are ways to optimize setting up a press brake that reduces waste and cost while ensuring high-quality results.
One way to improve efficiency is by automating certain processes within the setup procedure such as measuring components quickly with automated sensors or digitally controlling force output during operation. This eliminates guesswork from manual measurements or adjustments which can lead to mistakes and delays in production.
Additionally, these types of automation allow for faster cycle times between tasks which helps achieve more accurate products at higher speeds without sacrificing quality. Another way to increase productivity is through training staff on proper techniques when operating a press brake machine.
This ensures that operators have the necessary skillset needed for efficient use of equipment as well as understanding how different materials should be handled differently depending on their individual properties such as thickness, shape, or hardness level when bending metal pieces into their desired shapes. Proper instruction also allows workers to better identify potential errors before they happen saving valuable resources and increasing overall accuracy levels across all production runs.
Finally, investing in advanced software technology such as CAD/CAM systems can help streamline setup procedures even further allowing for quicker programing times while still providing precise results every time due to its built-in error checking abilities eliminating any possibility of human error from entering incorrect data manually into machines’ programs. With these strategies combined manufacturers will experience less downtime leading to increased productivity levels along with reduced costs associated with labor hours spent setting up presses brakes each day giving them a competitive advantage over other companies who don’t properly utilize these methods when producing car parts through press brakes operations.
How Automated Systems Enhance Quality Control in Car Parts Production with a Press Brake

The use of automated systems to enhance quality control in car parts production with a press brake is essential for setting the standard when it comes to accuracy. Automated systems help reduce the number of manual labor required while also providing consistent, reliable results that meet exact specifications every time.
The system keeps track of each part produced so that any inconsistencies can be identified and corrected quickly. By utilizing automated systems, the process becomes more efficient and accurate with less room for human error.
This helps ensure that all parts are produced at a high level of quality control which meets or exceeds industry standards. Additionally, these systems provide detailed reports on any discrepancies found during inspections allowing manufacturers to take corrective action as needed.
Automation has also helped improve safety in car part production by reducing potential risks associated with human errors such as incorrect measurements or misaligned pieces during assembly. Quality control personnel can monitor production remotely without exposing themselves to potentially hazardous environments, further improving efficiency and accuracy while keeping workers safe from harm’s way.
Overall, using an automated system for press brake operations provides many benefits when it comes to achieving high levels of accuracy in car parts production while ensuring safety and cost-effectiveness across the entire process
Conclusion
The use of press brake tooling in car parts manufacturing is essential to ensure accuracy and quality control. By setting the standard for precise measurements, press brakes help create reliable parts that meet industry standards.
As technology continues to advance, so do the capabilities of automated press brake systems; allowing for higher levels of accuracy with less human intervention. Quality control in car part production is paramount and having an accurate press brake helps achieve this goal efficiently and effectively every time.