Casting is a procedure in which a solid substance is dissolved, heated to an appropriate temperature, and then poured into a mold or cavity to solidify. Thus, any substance that can be dissolved is good to be used to make intricate or easy designs in only a single step. The final product can be configured in almost any way the designer desires.
Correct alloy, shape, size, structure, thickness, tolerance, and weight are critical in any casting technique. Magnetism, degradation, and stress distribution are other factors that influence the metal casting technique chosen. Scroll down to learn and understand the metal casting process.
Explaining The Metal Casting Procedure
We have listed a simplified summary of the metal casting process in the below section. However, remember that a few steps might differ for other casting variants.
1. Creating The Pattern
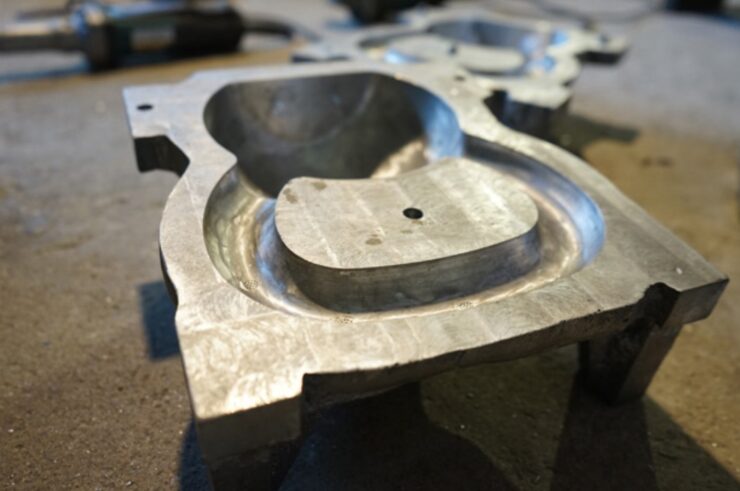
Several metal casting procedures begin with creating the pattern, a replica of the finished object used to make the mold. Patterns can be expendable or permanent, and they can be created out of wood, wax, and plastic.
2. Designing The Core
When casting hollow parts, a solid piece of core material should be placed inside the mold cavity to shape the interior geometry of the cast part. For instance, a cylinder core within a massive cylindrical mold will result in a tube-shaped cast item.
3. Creating The Mold
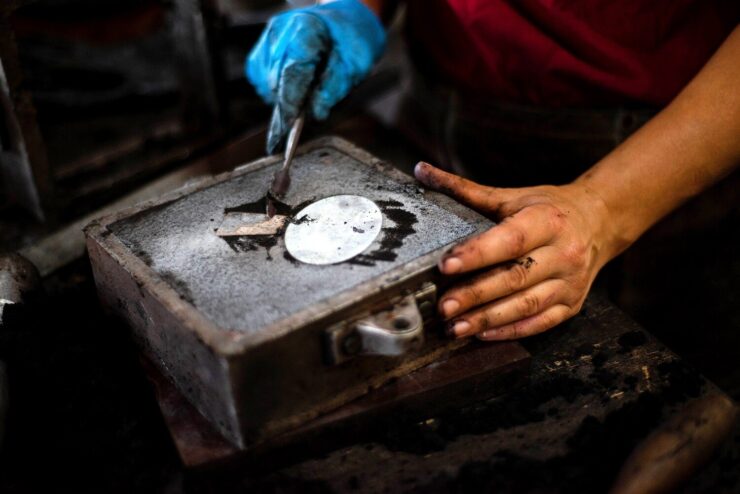
Molds are created in a variety of ways based on the technique. For instance, permanent metal molds can be created with a CNC machine, whereas sand molds are created by putting a sand mixture to the outside of a pattern. Mold making is a professional discipline that involves the fabrication of molds.
4. Filling the mold
After melting the metal, it is poured or forced into the mold. The molten material is spilled downside into the cavity in gravity casting. However, in high-pressure die casting, it is pressed into the hole at elevated pressure, and high clamping forces are necessary to keep the die secure.
5. Discarding The Part
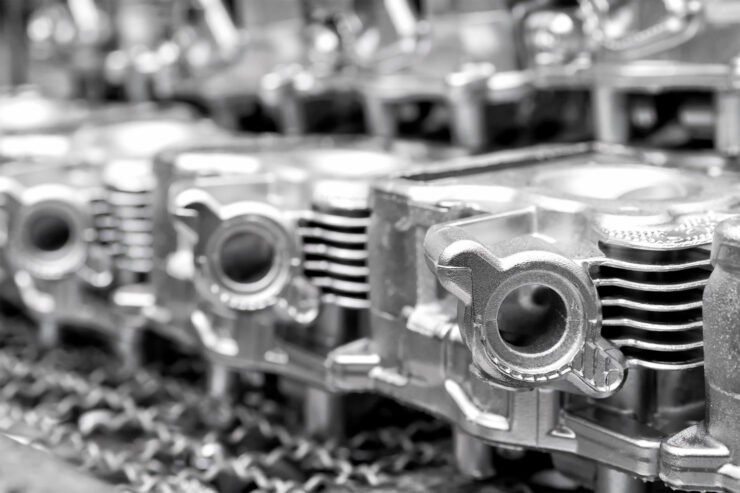
The cast portion is then removed from the mold after it has cooled and set. For sand casting, it requires demolishing the mold in order to obtain the part within. For permanent castings, the two sides of the metal mold are peeled apart and ready to be used again.
6. Cleaning
Before being used, cast metal components might require cleaning, which is necessary to remove mold remnants.
What Are Pros And Cons Of Metal Casting
Here are some of the advantages and disadvantages of metal casting:
Benefits Of Metal Casting
- Metal casting allows for the creation of complicated shapes.
- Casting is possible for almost all metals.
- A one-piece cast can yield crucial parts.
- Interior cavities and curved components can be cast.
- Casting can be used to make substances that are difficult or expensive to make using other methods.
- Casting is less costly than other manufacturing techniques for medium to massive orders.
Drawbacks Of Metal Casting
- The surface finish is somewhat coarse and is not suited for mating contacts.
- Metal casting, like shell molding has size and design limitations.
- Making patterns is time-consuming and costly
- Because of the increased rate of dies, die casting can be expensive for small to medium quantities.
What Are Different Types Of Metal Casting
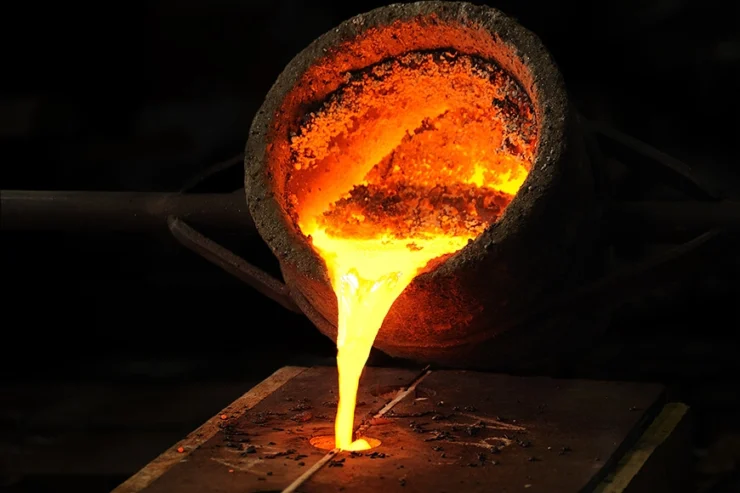
The essential nature of the mold design divides metal casting into two groups: expendable mold and permanent mold castings. You can visit https://dawangcasting.com/blog/types-of-casting-methods/ to know more about the different types of metal casting.
Permanent mold casting types include centrifugal casting, die casting, and gravity casting. The expendable mold casting contains sand casting, plaster molding, shell mold, ceramic mold, investment casting, and lost foam.
Permanent Mould Casting Types
- Centrifugal casting
Several casting processes that use rotational centrifugal forces to carry molten metal to the external sections of a circular mold cavity where it thickens to shape a product are known as centrifugal casting.
- Die casting
Die casting is another permanent mold metal casting technique. In this, liquid metal is poured into “dies” at varying pressures from 0.7 to 700 MPa and thickens as a metal cast.
- Gravity casting
In gravity casting, the molten material is poured into the mold from a crucible only by gravity.
Expendable Mould Casting Types
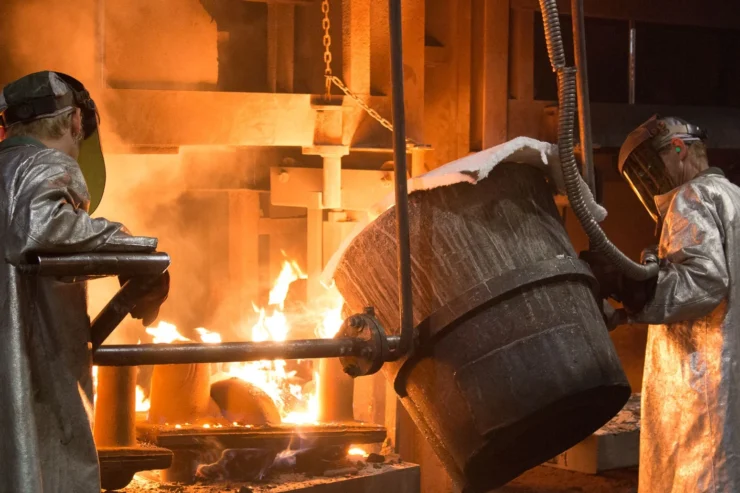
- Sand casting
The most prevalent type of expendable mold casting is sand casting, which uses permanent patterns to form the mold. With force or gravity, molten metal is spilled into an expendable sand mold cavity where it thickens to produce the cavity shape portion.
- Plaster mold casting
Plaster mold casting uses plaster of Paris rather than sand to create a mold that operates similarly to sand casting.
- Shell molding
Shell molding is done with a roughly 9 mm (3/8″) thin shell mold. A thermosetting resin binder is used to glue the mold together.
- Ceramic mold casting
Ceramic mold casting is comparable to sand or plaster mold casting. However, the only exception is that the mold is formed of refractory ceramic material. In comparison to the plaster mold, the ceramic substance can resist high temperatures. As a result, it is utilized to make cast steels, cast irons, and various high-temperature alloys.
- Investment casting
A wax pattern is garnished with a refractory substance to form a mold. After that, it is melted away before molten metal is spilled into the cavity to thicken.
- Lost foam casting
A polystyrene foam pattern is utilized to build a sand mold in lost foam casting. When molten metal spills into the mold, the design vanishes. Expanded polystyrene casting, evaporative foam casting, and lost pattern technique are other names used to describe lost foam casting.
Bottom Line
As you can see, heating a metal, spilling it into a mold, waiting to cool and thicken, and then extracting the final item from the mold is the fundamental metal casting process. In practice, the procedure might have several more phases. In addition to that, you have to remember that different metal casting methods operate in different ways.