In the world of warehousing, space is one of the most valuable assets. Whether you’re running a small distribution centre or a large-scale storage facility, optimising your available space can make a significant difference in both operational efficiency and profitability. That’s where pallet racking comes into play.
Pallet racking systems offer a robust and scalable way to store goods vertically, freeing up floor space and making warehouse operations more organised and efficient. By implementing the right racking setup, businesses can improve inventory management, speed up order fulfilment, and increase safety across the warehouse.
What is Pallet Racking?
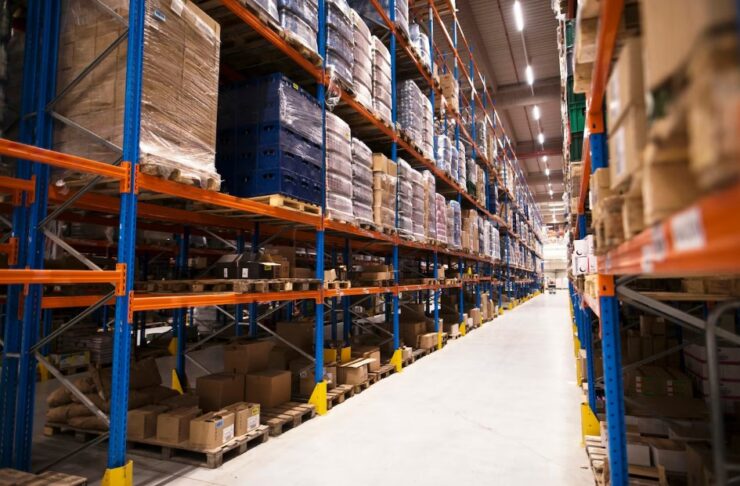
Pallet racking is a material handling system designed to store goods on pallets (or “skids”) in multiple horizontal rows and vertical levels. These systems are typically made from steel and are engineered to withstand heavy loads, making them ideal for industrial environments. Depending on your warehouse layout and operational needs, different types of racking can be installed, from selective pallet racking to drive-in, push-back or cantilever racking.
Why Pallet Racking is Essential for Modern Warehousing
As the demand for faster delivery and larger product ranges grows, warehouses must evolve to handle more stock without necessarily expanding their footprint. Pallet racking provides a cost-effective solution to this challenge. It allows companies to stack goods safely and access them quickly using forklifts or other warehouse equipment.
Moreover, racking systems support inventory accuracy. When goods are stored in designated, well-labelled locations, warehouse staff can locate items more quickly, reducing errors and improving productivity.
Choosing the Right Type of Pallet Racking
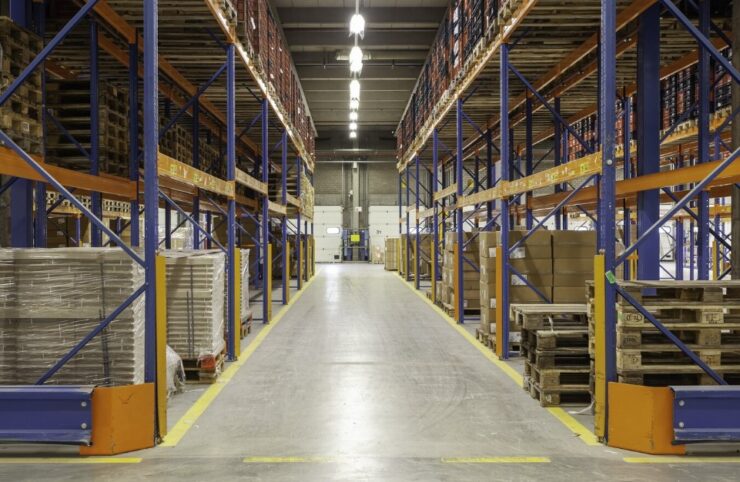
Not all pallet racking is the same, and choosing the right system depends on factors such as the type of goods being stored, available space, forklift access and desired storage density. Here’s a brief overview of common racking types:
- Selective Racking – Ideal for high SKU counts and first-in, first-out (FIFO) inventory systems. It offers direct access to each pallet but requires more aisle space.
- Drive-In Racking – Suitable for last-in, first-out (LIFO) stock where pallets of the same type are stored in high volumes.
- Push-Back Racking – Offers a high-density solution with multiple pallets stored in each lane, accessible from one side.
- Cantilever Racking – Designed for long or irregularly shaped items like timber or pipes.
Enhancing Safety and Compliance
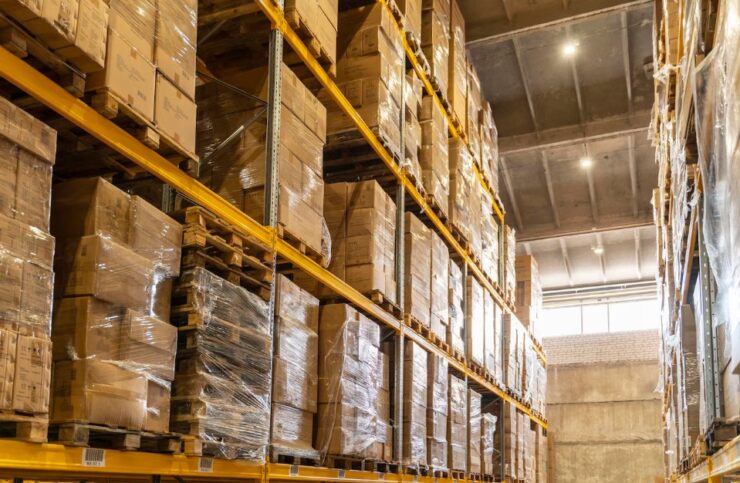
Warehouse safety is paramount, and pallet racking for warehouses must be installed and maintained correctly to avoid accidents. Regular inspections are essential to identify structural damage, overloading, or incorrect use. It’s also important to ensure that racking complies with British safety standards, such as SEMA (Storage Equipment Manufacturers Association) guidelines.
Investing in proper training for staff and carrying out regular risk assessments will further reduce the likelihood of accidents and maintain the integrity of the racking system.
A Long-Term Investment in Efficiency
For businesses looking to scale or streamline their operations, pallet racking is a practical and future-proof investment. It supports better stock rotation, makes picking and packing more efficient, and ensures every inch of warehouse space is used to its full potential. As e-commerce and logistics continue to grow, having a flexible and reliable storage system in place is no longer optional — it’s essential.
If you’re planning to upgrade your warehouse or build a new storage facility, consulting with a professional racking supplier can help ensure you select a system that fits your current needs while allowing room for future growth.