As humans continue to strive for a more sustainable future, steel casting remains at the forefront of industrial progress. Steel casting is an important process that has been used in many industries throughout history and continues to be relied on today. While it can create strong and durable products, it also comes with its own set of environmental impacts due to unsustainable practices and the lack of recycling opportunities.
This article will explore the environmental impact of steel casting, particularly when it comes to sustainability and recycling efforts. It will discuss how advancements in technology have allowed us to reduce waste while still producing high-quality products through innovative methods like 3D printing processes.
Additionally, this article will look into how new initiatives are attempting to increase awareness about the importance of recycling casted steel materials to protect our environment from further damage. Ultimately, this article seeks to provide readers with an understanding of why sustainability and recycling should be taken seriously when discussing modern manufacturing practices related to steel casting.
Analyzing the Sustainability of Steel Casting
Steel casting is one of the most important processes in modern manufacturing. It enables the production of complex, precision parts with outstanding strength and durability that are often impossible to achieve through other processes. However, when it comes to sustainability and environmental impact, steel casting has its drawbacks. This article will analyze the sustainability of steel casting in terms of resource consumption, energy use, emissions generated during production, and reusability or recycling options available.
The process begins with melting down scrap metal into liquid form at high temperatures using either an electric arc furnace (EAF) or cupola furnace technology. The heated molten metal is then poured into a prepared mold which contains a pattern for the desired parts\’ shape; this step requires large amounts of heat and power resources as well as specialized equipment resulting in considerable overhead costs associated with staff training and maintenance expenses on top of costly raw material ingredients such as iron ore, coke, limestone flux, etc., all contributing to an overall environmental burden related to steel casting operations.
Further complicating matters is the fact that many byproducts created during production contain hazardous substances like slag which can be difficult to dispose of safely without causing further damage due to potential leaching into groundwater sources if not handled properly. Additionally, depending on the complexity of the part design required there may also be additional issues regarding machining operations needed after castings have been completed adding another layer of engineering expertise necessary for successful project completion but also increasing energy usage throughout the entire product life cycle until eventual disposal occurs requiring careful consideration when analyzing sustainability implications from a full-lifecycle perspective.
Exploring Recycling Options for Steel Castings
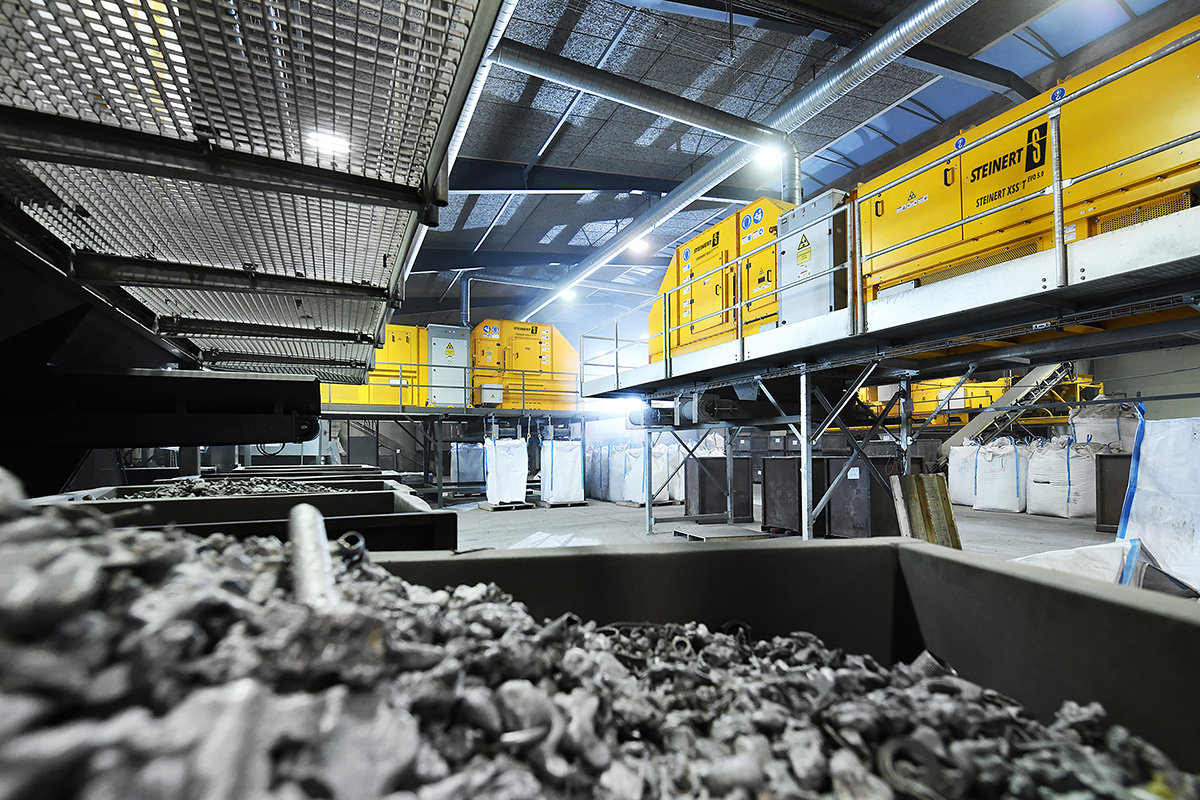
Steel casting has a significant environmental impact, and sustainability is key to reducing its effects. Fortunately, there are several options for recycling steel castings and their byproducts, which can reduce the overall carbon footprint associated with these processes. For those looking for more efficient ways of managing their steel casting waste, the most popular option is to melt down used castings and reuse them in new products.
This process reduces both energy costs and emissions associated with the production of new material from scratch. Additionally, this approach minimizes the number of additional resources needed during manufacturing processes due to less raw material being required. Another alternative is reusing existing steel parts without melting them down first – either as-is or refurbished through machining operations such as grinding or sanding down surfaces. In cases where a part cannot be reused directly but still contains valuable materials inside it (such as copper or lead alloys), the piece can be cut open so that individual components can be extracted separately before being recycled accordingly.
Finally, another effective way to recycle steel castings would involve repurposing older pieces into artwork or other creative projects; this approach requires minimal extra resources while also providing an aesthetic advantage over simply disposing of items in landfills or incinerators after they have reached end-of-life status. By taking up any one (or multiple) of these approaches when dealing with obsolete metal objects from production processes, companies will not only improve their bottom line but also benefit society at large by ensuring sustainable disposal practices are put into place!
Reducing Carbon Emissions through Sustainable Practices
Steel casting is a process that has been used for centuries and continues to be an important part of many manufacturing processes today. However, it can also have a significant environmental impact due to the high energy usage and emissions associated with the production of steel. Reducing carbon emissions through sustainable practices is one way to reduce this impact, as well as make steel production more environmentally friendly. Implementing energy-efficient processes in steel casting facilities can help decrease the amount of energy needed during the manufacturing process.
This could include using renewable or clean sources such as solar power or wind turbines, which would reduce reliance on traditional fossil fuels. Additionally, switching from coal-fired furnaces to electric arc furnaces could reduce greenhouse gas emissions significantly by using electricity instead of burning coal. Further improvements include utilizing technology such as 3D printing for mold making which reduces material waste and shortens lead times when producing complex parts quickly and accurately.
Recycling scrap metal is another great way to improve sustainability in steel casting operations while reducing overall environmental impacts by reusing materials already available instead of creating new ones from scratch; resulting in less energy consumption, fewer chemicals released into the environment, and lower costs for producers compared with buying new raw materials each time they need them produced again.
Finally, providing employees with education about their role in contributing towards sustainability efforts within their facility will ensure everyone understands how their collective actions directly affect day-to-day operations and long-term goals related to reducing carbon emissions through sustainable practices implemented at each stage of production within the facility itself.
