Aluminum extrusions are an essential part of modern design and fabrication. From industrial components to everyday objects, aluminum extrusions can be used in a wide range of applications.
For those looking to get the most out of their aluminum extrusion projects, here is a comprehensive look at Aluminum Extrusions 101: Essential Tips for Design and Fabrication. Learn about the best practices for designing with aluminum, material selection tips, fabrication techniques, and more – all in one place! Whether you’re new to using aluminum or an experienced professional designer/fabricator this guide will help you make informed decisions that lead to successful projects every time.
Fabrication Techniques for Aluminum Extrusions
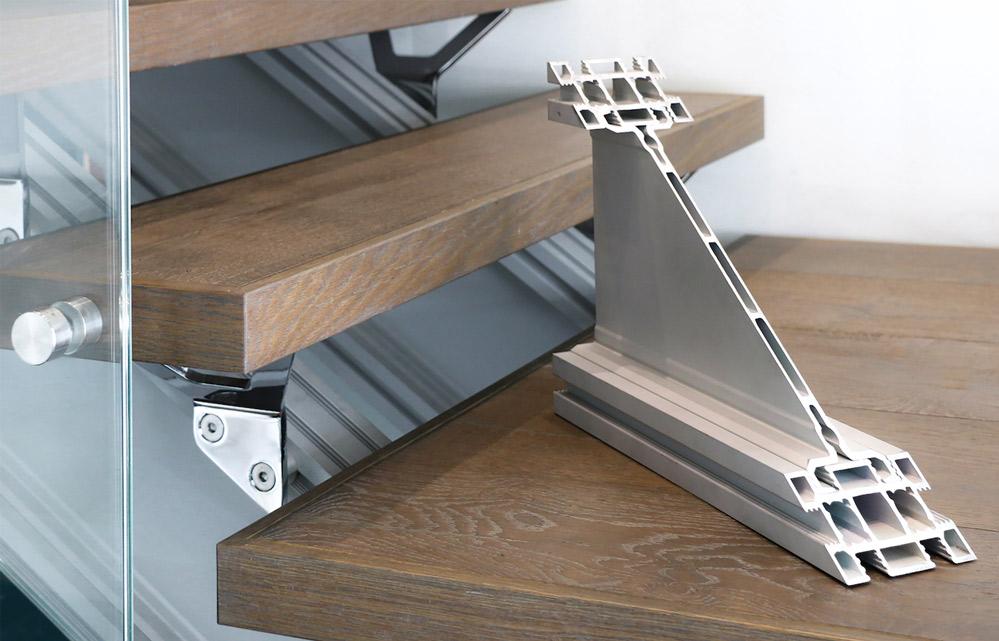
Aluminum extrusions offer vast possibilities for design, fabrication, and manufacturing. When it comes to fabrication techniques specifically for aluminum extrusions, there are several methods available that have been developed over the years.
These techniques typically involve cutting extruded shapes from aluminum bars or rods with specialized machinery to create components of varying sizes and shapes. Some of these methods include hot sawing, cold sawing, punching and piercing, shearing, slotting, and notching.
Hot sawing is a common technique used when making small parts out of extruded aluminum as it involves using a high-speed circular blade to cut through the material at a relatively fast rate while creating minimal heat distortion on the final product. Cold sawing is also employed for small parts but often yields a cleaner edge than hot sawing due to its much slower cutting speed which produces next to no heat distortion on finished pieces.
Punching and piercing are two different processes that use tools such as dies or punches respectively to form holes in an extrusion profile while allowing flexibility in terms of size and shape customization. Shearing is another popular method used when fabricating larger components requiring straight cuts along lengthwise lines; this process uses scissors-like blades which produce smooth edges without any additional finishing required afterward due to their precision accuracy during operation time.
Slotting provides more intricate designs featuring slots rather than simple holes or cuts by using special grooved blades while Notching creates unique angles in profiles by utilizing inverted V-shaped blades which can be adjusted depending on desired outcome requirements per job type.
Finishing Options for Aluminum Extrusion Projects
Finishing options for aluminum extrusion projects can be as diverse as the projects themselves. From powder coating and anodizing to painting, there are many ways to finish a project with aluminum extrusions.
Powder coating provides a durable and attractive finish that is resistant to corrosion, impacts, weathering, and wear and tear. Anodizing involves applying an electric current to create a protective oxide layer on the surface of the metal which helps protect it from corrosion while also providing a decorative look.
Painting with liquid coatings can provide vivid colors that may not be possible with other finishing techniques but should only be used if long-term durability isn’t required due to its potential for chipping or flaking over time. Whatever your desired outcome might be when it comes to completing an aluminum extrusion project, there’s likely a suitable finishing option available that will help you achieve great results.
Benefits of Utilizing Aluminum Extrusions in Your Designs

Aluminum extrusions offer designers and fabricators a multitude of benefits. From lightweight construction to excellent corrosion resistance, aluminum extrusions have become an essential part of many designs.
Utilizing aluminum extrusions in your design can provide additional strength and stability while simultaneously reducing weight when compared to other materials. The wide selection of shapes available allows for greater flexibility in design options as well as the ability to customize a solution that is tailored to each project’s needs.
Aluminum also offers superior thermal conductivity which helps reduce energy costs by allowing heat transfer more efficiently than other materials such as steel or plastics. In addition, extruded aluminum is easy to work with due to its malleability which makes it ideal for creating complex parts like curves and angles with ease.
Finally, aluminum extrusions are cost-effective and require minimal maintenance over their lifetime making them the perfect choice for any designer or fabricator looking to save time and money on their next project!
Conclusion
Aluminum extrusions are an incredibly versatile material and have many applications, from windows to door frames to automotive components. Aluminum extrusions can be used in a variety of design and fabrication projects, from simple structures to complex designs.
When it comes to aluminum extrusion fabrication, several essential tips should be kept in mind for successful outcomes. These include selecting the right alloy grade for the application; using proper tools and equipment; designing profiles with draft angles; accounting for thermal expansion coefficients during assembly; allowing sufficient clearance between parts to prevent binding due to differential thermal expansion rates; understanding CAD modeling software best practices when creating 3D parts; and considering trailer aluminum extrusions as a cost-effective alternative. By utilizing these tips designers and fabricators will find themselves better able to create quality results from their aluminum extrusion projects.